The first EV to go on sale in the U.S. might have been way back in the 1890s, but it’s not been until more recently that the tech has taken off and been adopted by America’s motorists. Now, battery-powered models account for six percent of new car sales in the States and around three percent of all vehicles assembled here.
But while the tech might still be relatively new, there is still a steady stream of battery-powered cars being taken off the road and into the scrap heap. Whether it’s due to damage in a collision or simply because something newer and more efficient has come along, all cars meet their end eventually.
With a gas-powered car, the metals that make up the engine, transmission and body panels can all be stripped out and recycled, as can some materials used inside the car. And while the same process is true for a lot of EV components, there’s one essential part that requires a new approach when it comes to recycling: the battery.
In an EV battery, you’ll find a complex array of positively-charged cathodes, made from metals like lithium, nickel and cobalt, and negatively-charged anodes comprising materials like graphite. These are expensive elements of which there is a finite amount here on Earth. So simply dumping an EV battery in the trash isn’t an option.
Instead, companies have been looking into ways to reclaim and recycle these metals, with the aim of eventually putting them to use in brand new batteries that can power the next generation of electric cars. Now, YouTuber Zack Nelson who runs the JerryRigEverything channel has taken a look inside one of the factories working to do just that.
The video, which is linked above, shows how U.S.-based Li-Cycle breaks EV batteries down into the plastics and metals that make them up, ready to be recycled and reused once again.
At the start of the process, a waste battery from an electric car is loaded onto a conveyor that takes it to the top of a machine. Nelson explains that the battery is then passed through a sort of shredder, which is flooded with a special liquid that prevents the whole process from ending in disaster.
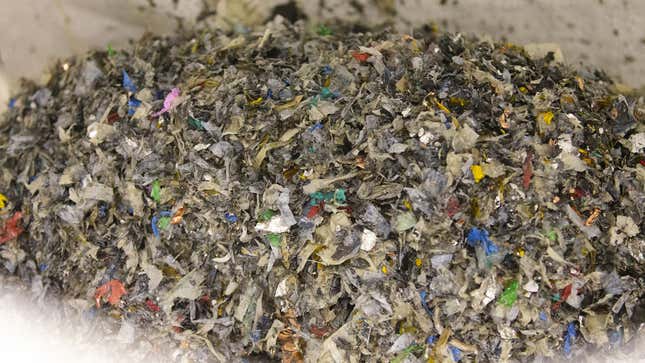
Once the battery has passed through the shredder, it completely loses its charge and the whole thing becomes an inert mass of different materials. To separate all the constituent components out, Li-Cycle uses vibrating plates to first remove all the plastic from the slurry.
Next, the metals like copper, steel and aluminum sink to the bottom of the slurry where they can then be siphoned off and collected for further processing. The final step sees the remaining liquid pass through a filter press, which uses high pressure to separate dissolved solids from the liquid. This step allows Li-Cycle to collect the lithium, nickel and cobalt that are found in most EV batteries.
These metals are clumped together in a substance the company calls “black mass,” which it says can then be further refined so that these materials can one day be used to create new batteries. To do this, Li-Cycle is working to open a processing facility in Rochester, New York, where it will be able to process up to 35,000 tonnes of black mass per year

The process is fascinating, and means that up to 95 percent of the material that goes into an EV battery can be stripped down and fully recycled, which is pretty impressive considering the environmental impact of mining such materials new.